Hello experts!
I was exploring the new feature in manufacturing process which has been in general availability (but in preview) since June 7th (10.0.40). If you aware about this feature it makes possible to track and trace serial and butch numbers of components used in production and link them to serial and batch numbers of finished goods (even for production orders with quantities exceeding one unit).
I find this feature very promising to reduce efforts and labor during manufacturing accounting. But in the course of my investigation, I came across the problem of calculating the cost of finished products.
Let me share the details of the case I’ve tested.
First of all, I created a BOM:
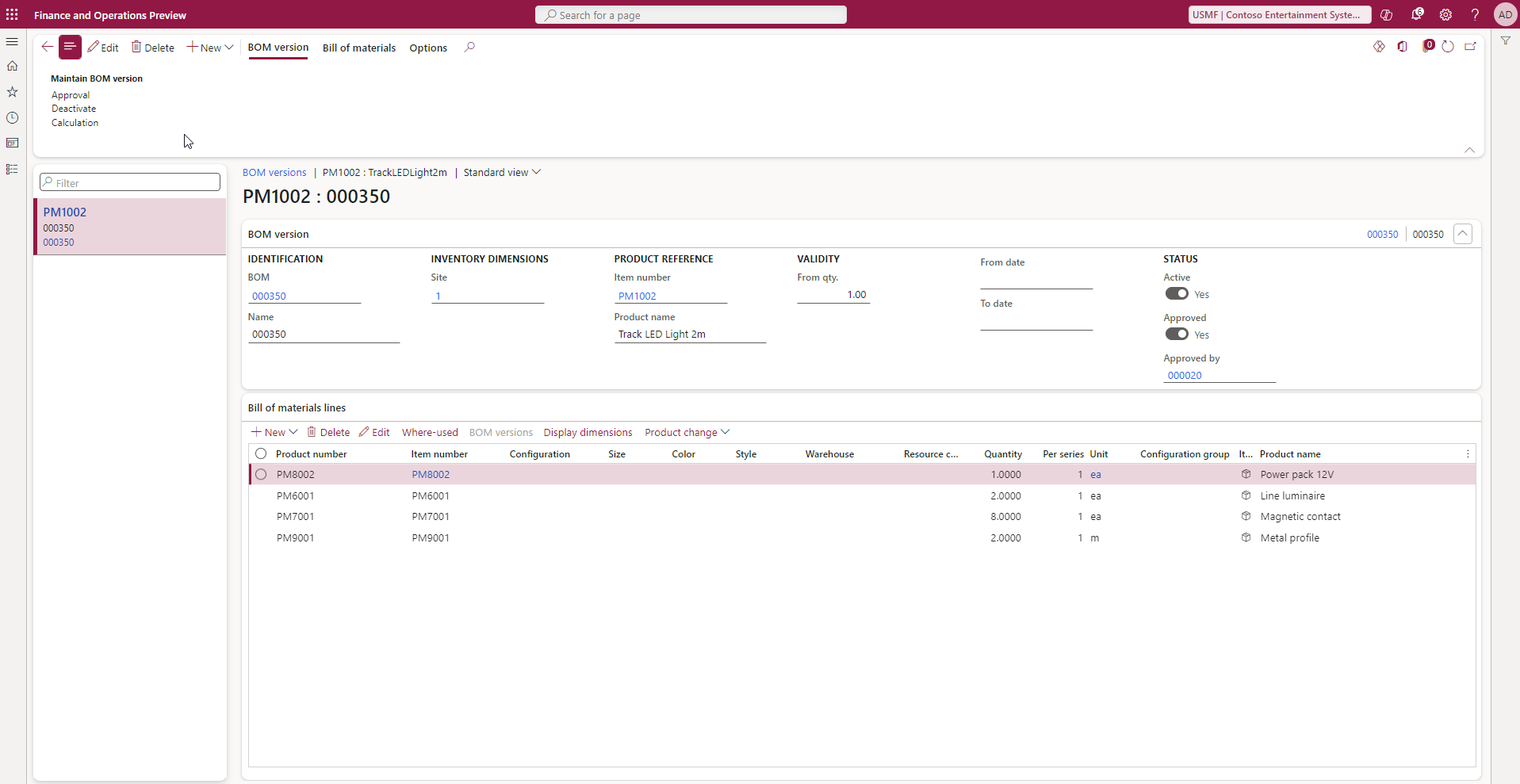
Then, I invoiced purchase orders for all components. I’ll not share all of them here, but only one where I brought the same item (PM8002) in different price. Also, for this Item I’ve created a special Tracking dimension group where Batch Number dimension used for Financial inventory:
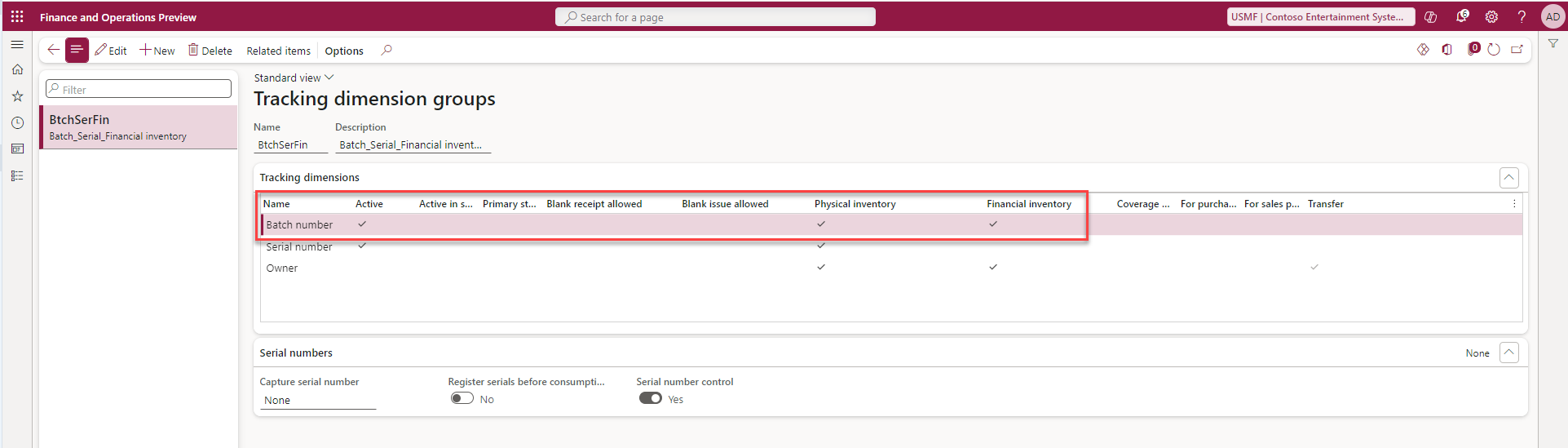
And those are transaction details for the components I used in manufacturing:


So, as you may see there are different cos amounts for different Butch Number.
Then, I’ve created a production order for 2 units. This is the Picking List journal. You can see the same Butch numbers in it:

Using the new “Tracked components” form I’ve associated finished goods with serial and butch numbers of components (finished goods also has the Tracking Dimension group with financial inventory for Butch number dimension):
First piece:
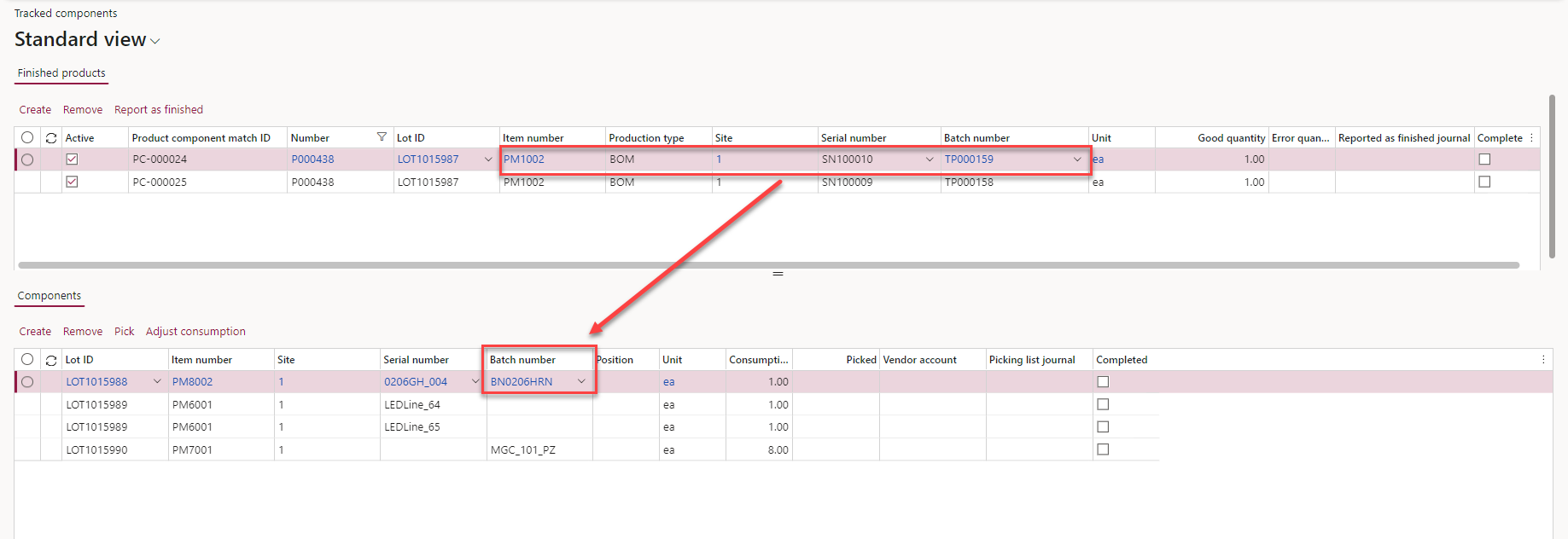
Second piece:
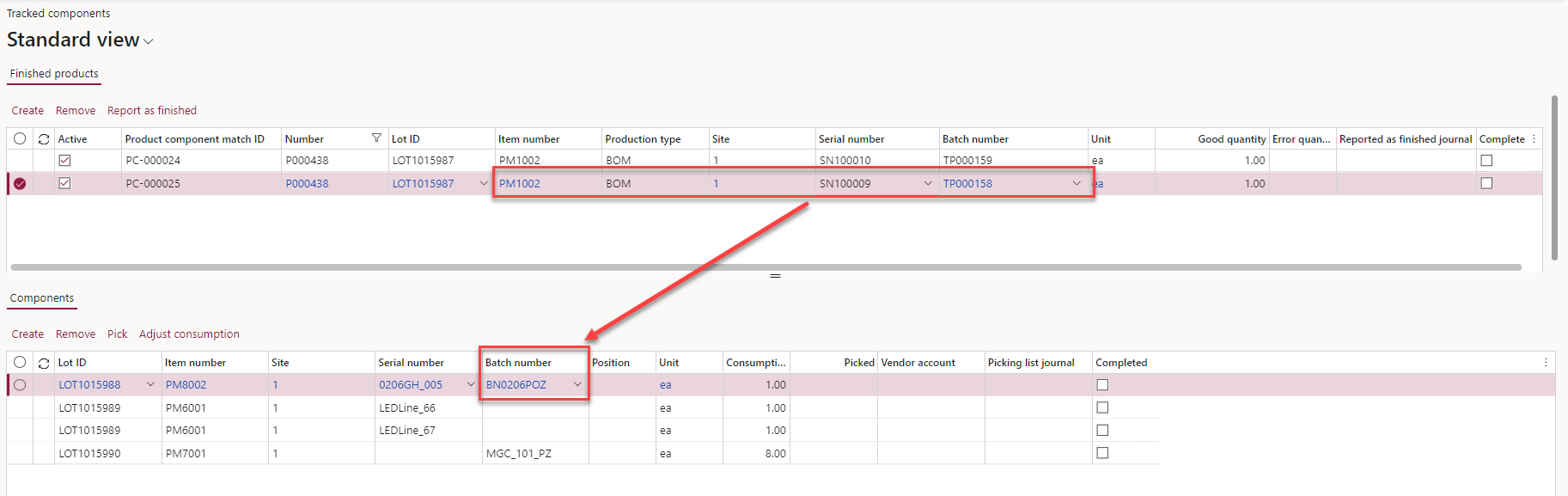
I’ve processed the production order for the End status to calculate cost amounts for finished goods. But both pieces have the same cost amount:

If we are going to take a look on financial voucher then we’ll see that material costs are absolutely the same for both lines and calculated as average cost for PM8002 item instead of FIFO like it settled in Item Model Group.
So, from my point of view looks like it doesn’t work correct. Does somebody have opinion on this case? I’ll be please on any assist with this question, because without correct cost accounting it seems useless.
I was exploring the new feature in manufacturing process which has been in general availability (but in preview) since June 7th (10.0.40). If you aware about this feature it makes possible to track and trace serial and butch numbers of components used in production and link them to serial and batch numbers of finished goods (even for production orders with quantities exceeding one unit).
I find this feature very promising to reduce efforts and labor during manufacturing accounting. But in the course of my investigation, I came across the problem of calculating the cost of finished products.
Let me share the details of the case I’ve tested.
First of all, I created a BOM:
Then, I invoiced purchase orders for all components. I’ll not share all of them here, but only one where I brought the same item (PM8002) in different price. Also, for this Item I’ve created a special Tracking dimension group where Batch Number dimension used for Financial inventory:
And those are transaction details for the components I used in manufacturing:
So, as you may see there are different cos amounts for different Butch Number.
Then, I’ve created a production order for 2 units. This is the Picking List journal. You can see the same Butch numbers in it:
Using the new “Tracked components” form I’ve associated finished goods with serial and butch numbers of components (finished goods also has the Tracking Dimension group with financial inventory for Butch number dimension):
First piece:
Second piece:
I’ve processed the production order for the End status to calculate cost amounts for finished goods. But both pieces have the same cost amount:
If we are going to take a look on financial voucher then we’ll see that material costs are absolutely the same for both lines and calculated as average cost for PM8002 item instead of FIFO like it settled in Item Model Group.
So, from my point of view looks like it doesn’t work correct. Does somebody have opinion on this case? I’ll be please on any assist with this question, because without correct cost accounting it seems useless.
Categories: